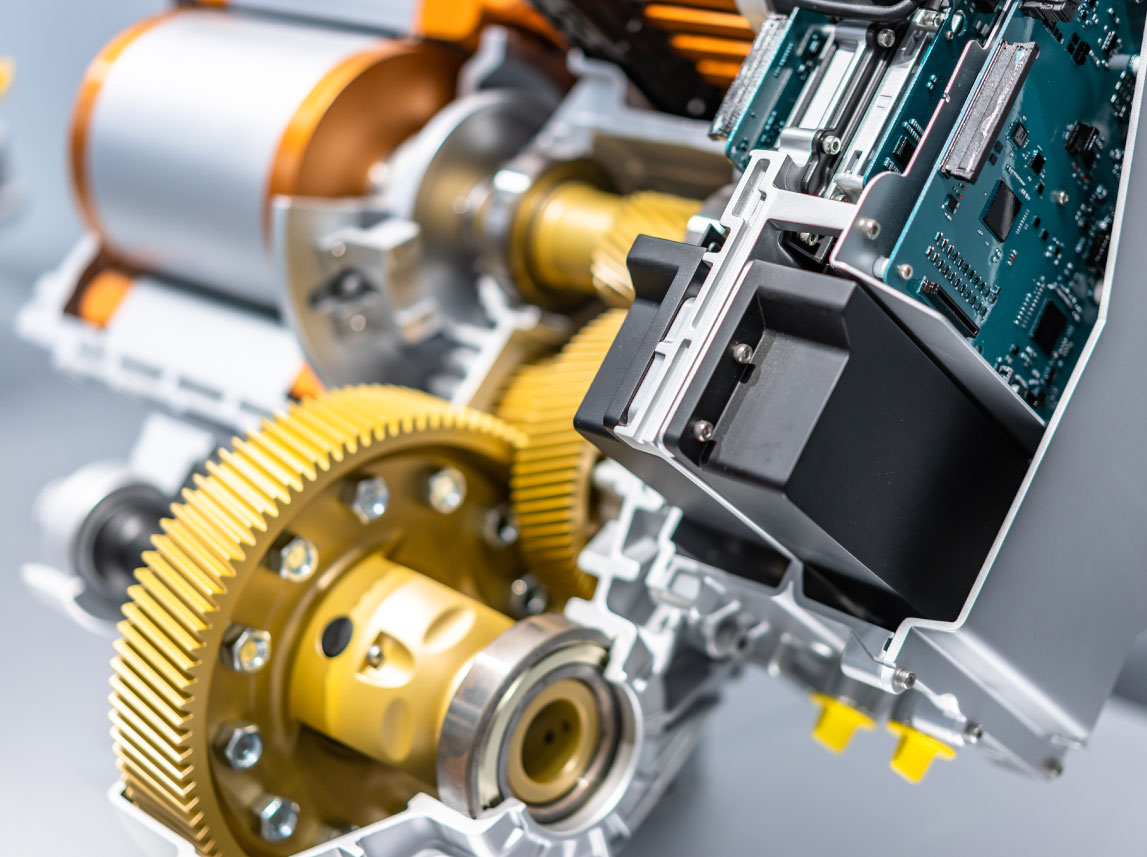
11 Jan EV Powertrain Development Milestone
KBE+ has just completed its fifth powertrain design and development for an all-electric vehicle application for a yet another new client.
KBE+, Inc. has just completed its fifth powertrain design and development project for an EV (Electric Vehicle). This represents a milestone in our development efforts to become a premiere provider electric axle or powertrain designs. Our portfolio now includes;
- A single-speed, single-stage transaxle
- A single-speed, multi-stage transaxle
- An e-axle (integrated electric motor into the axle housing)
- And finally, a multi-speed, multi-stage transaxle
In addition to the common design requirements of any electric drive product, that of;
- High efficiency
- Long service life
- Ability to deal with maximum torque anywhere in the operational speed range
KBE+ was tasked with developing designs that were far more quiet (low NVH qualities) than typically geartrains in the automotive spaces usually require. This required a multi-phased approach to gear geometry development, many iterations in terms of predicting transmission error, and both material and lubricant selections that were not the common choices made for automotive applications.
We have also done a great deal of work with Powdered Metal (PM) and its native ability to dampen certain frequencies and reduce the magnitude of vibration across the frequency spectrum. PM affords not only an ease of manufacturing, but also the ability to generate part geometry that would otherwise not be viable in the traditional wrought and cut approach. Use of PM as the complete gear or as part of the gear support (the blank or web) also provides a means to tailor the mode shapes and the modal response frequencies to optimize specific applications. Please contact us if you have any questions or would like to know more about our services and expertise.
Sorry, the comment form is closed at this time.