
05 May The Analysis, Design and Development of an Automated Manual Transmission (AMT) Using Powder Metal (PM) Gears
When accounted for in the design development, Powder Metal (PM) is a viable alternative to traditional cut steel.
Höganäs partnered with KBE+, Inc. to reverse engineer a modern Automated Manual Transmission (AMT). Once the design was fairly well understood and a duty cycle had been developed based on real-world driving and the Worldwide Harmonized Light vehicles Test Procedures (WLTP), the project focused on deriving a replacement transmission gearset that would satisfactory service life, provide essentially the same efficiency, and with reduced rotational inertia made from Powder Metal (PM).
The project had four main objectives;
- Determine the viability of PM as a material for the gears to be used in an automotive transmission
- Develop a methodology to develop viable gears for an automotive application
- Determine if the natural dampen characteristics of PM can used effectively in a dynamic application
- Make a set of prototype gears, build them into the existing transmission case (thus of similar size of the cut and heat-treated OEM gears) and then validate all assumptions and design techniques used to create these transmission gears
A common belief is that PM parts in the automotive sector were cost effective to produce in large quantities but lacked the strength needed to serve as load bearing gears in a transmission. Advances in compaction presses and tooling, as well as PM mixes and additives, enabled higher densities and more complex part geometries. The Smart project was spearheaded by Höganäs headquartered in Sweden. To facilitate highly effective collaboration one of their top research scientists relocated to the United States and work with the design team at KBE+, Inc. The projected started with the teardown and redesign of the transmission from a 2008 Smart ForTwo. The car is small, only 2.7 meters long and weighs in at a modest 820 kg. However, the engine still pumps out decent power at 70 (hp) and 92.2 (Nm) torque. All that power is handled by a 5-speed AMT, a manual transmission with servos handling both shifting and the clutch.
After the teardown and subsequent measuring and analyzing of the gears, a transmission model was created and used to make PM optimized gear designs. Seven gears in total were converted to PM, some gears like the first and second input gears were machined on the input shaft and hence not possible to convert. The material of choice was Astaloy 85 Mo with 0.3% graphite, a well-known and commonly used material within the PM industry.
Designing gears made from PM is different compared to designing gears for solid steels due to the variations in material properties. The material parameters differ depending on the material composition, density and secondary operations like heat treatment or surface densification. Höganäs makes these parameters complete with SN curves available for partners interested in PM gears. All this data along with power transfer requirements and required service life is put into a gear design software by a transmission design engineer and out comes a gear optimized for PM. Additionally, PM offers additional design freedom such as tooth root design that in conventional gear cutting is decided by the cutting motion of the hob that cuts the gear teeth and cannot be modified. With PM an optimal root shape can be used that enables a stress reduction in the gear tooth root, we have seen stresses lowered by 40% in some cases.
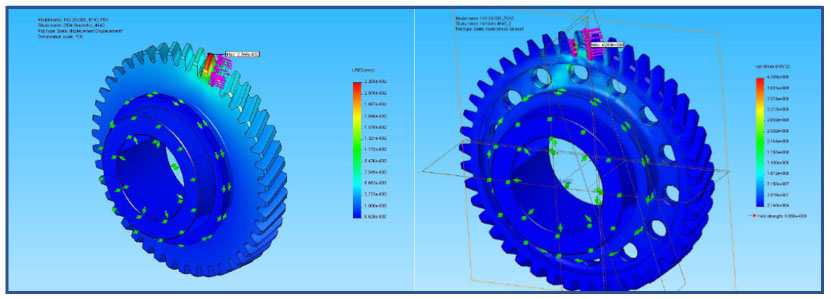
A gear in the Smart transmission before and after PM optimization.
In summary, a weight saving of 15.0% and a reduction in inertia of 14.9% was possible through a combination of weight saving design and lower density of the PM gears over the OEM cut steel gears. All PM gears were manufactured from compacted and sintered blanks using conventional gear cutting processes. The cut gears were then heat-treated using gas carburization and oil quenching before finish grinding. Due to the internal porosity of not fully dense PM, standard steel heat treatment recipes cannot be used, the carburizing gas travels much faster into the PM part and shorter cycle times are therefore needed.
A complete transmission with the seven PM optimized gears was built and mounted in a Smart ForTwo. The car continues to be driven in a real-world environment and has collected in excess of 200,000 (km) to-date. At the end of the 200,000 (km) drive the gearbox was removed from the car and disassembled. The post drive test revealed minimal wear or any other adverse effects to the transmissions as a function of the use of PM. KBE+ continues to use PM in gear designs, continues to develop new and novel design and analysis techniques and champion the use of PM with its clients.
Sorry, the comment form is closed at this time.